分析碳素與滲碳鋼的疲勞性能時(shí)涉及到殘余內(nèi)應(yīng)力和表面強(qiáng)化工藝的影響。但是滲碳零件的殘余內(nèi)應(yīng)力的分布和強(qiáng)化工藝對(duì)其疲勞性能的影響重要了,所以我們對(duì)它進(jìn)行專門的討論。
(1)滲碳零件的殘余內(nèi)應(yīng)兒凸零件經(jīng)滲碳淬火后在滲碳層會(huì)引起很大的殘余壓力,引起殘余壓應(yīng)力的原因是由于滲碳層各部位含碳量小同因而在淬火過程。
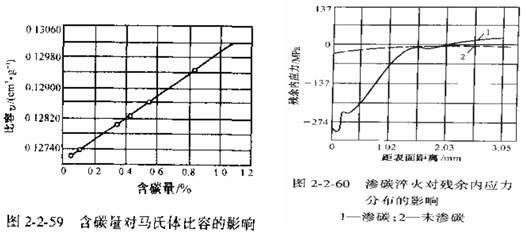
引起不同的體積變化:馬氏休的比容和其中含碳址的火系示于圖2-2-59。從圖可以看出:含碳量為0.1%-0.20%的心部和含碳量為O.9%一1.2%的滲碳層的比容之差為2.0%~2.5%在這種相對(duì)體積變化的影響下,在滲碳層引起殘余壓應(yīng)力,而在心都引起殘余拉應(yīng)力。殘余壓應(yīng)力,而在心都引起殘余拉應(yīng)力。圖2-2-59含碳量對(duì)馬氏體比容的影響零件滲碳淬火后在滲碳層中存在有殘余壓應(yīng)力很容易探究,例如將12.5mm×12.5mm的方形試樣。二對(duì)面耐滲碳淬火,然后將試樣沿縱向在不滲碳的面處切開,則發(fā)現(xiàn)切開的里(陽切開的面)產(chǎn)生彎曲變形,這就是由于滲碳淬火后在滲碳層產(chǎn)生殘余壓應(yīng)力的結(jié)果:
用SAE8617鋼(0.20%C,0.90%Mn,0.30%Si.0.71%Cr.0-67% Ni,0.11%Mo)進(jìn)行了試驗(yàn),解滲碳對(duì)殘余內(nèi)應(yīng)力分布的影響。試驗(yàn)樣品直徑為19.05mm( 0.75mm),樣品長(zhǎng)度一半鍍銅后在925℃氣體滲碳6h,鍍銅部分未滲碳,而未鍍銅部分滲碳得到的滲碳層厚為1.13-1.27mm,滲碳后直接淬45℃油,樣品未經(jīng)問火,滲碳部分和未滲碳郎分(鍍銅部分)的殘余內(nèi)應(yīng)力分布情況示于圖2-2-60,滲碳淬火后可以顯著地改變樣品表而的殘余內(nèi)應(yīng)力分布情況,表層產(chǎn)生很大的殘余壓應(yīng)力。弘超在這里為廣大用戶朋友提供有關(guān)滲碳鋼的相關(guān)資訊,以及合金鋼、碳鋼等確切的信息,很多因素影響滲碳件殘余內(nèi)應(yīng)力的分布情況,例如,橫斷面中滲碳層而積和整個(gè)樣品橫截面積的比值、滲碳層的金相組織和回火溫度等都對(duì)滲碳零件的內(nèi)應(yīng)力分布特征有影響。
表1-1-1列出樣品尺寸對(duì)滲碳樣品殘余內(nèi)應(yīng)力的影響。當(dāng)樣品尺寸改變而滲碳層厚度不變時(shí)即改變了滲碳層面積與整個(gè)樣品橫截面積的比值,樣品尺小縮小即增加,該比值,該比值增加(樣品尺寸不變滲碳層厚增加或滲碳層厚不變樣品尺寸縮?。┍韺託堄鄩簯?yīng)力降低而心部拉應(yīng)力增加。
1.滲碳層金相組織對(duì)其殘余內(nèi)應(yīng)力的分布也有影響,金相封組織中有碳化物存在將促使表面比容增加,就增加表面殘余壓應(yīng)力,金相組織中殘余奧氏體數(shù)量增加將促使?jié)B碳層的就能減小,因而降低表層的殘余應(yīng)力。滲碳淬火后回火對(duì)殘余應(yīng)力也有影響,回火溫度升高表面的殘余壓應(yīng)力和心部的殘余拉應(yīng)力的數(shù)值都降低,而且表示殘余壓應(yīng)力降低的更為顯著。
2.表面強(qiáng)化工藝對(duì)殘余內(nèi)應(yīng)句分布及疲勞性能的影響:表面強(qiáng)化工藝主要有滾壓強(qiáng)化與噴丸強(qiáng)化二種。滾壓強(qiáng)化是用輥?zhàn)踊蚯蛎娴臐L動(dòng)對(duì)零件表面施加滾壓的力,它對(duì)于有圓角或溝槽的零件在該部位進(jìn)行強(qiáng)化最為有效;噴丸強(qiáng)化就是高速向零件表面噴射硬的鋼丸而對(duì)零什進(jìn)行強(qiáng)化,它適用于整個(gè)零件表面都需要強(qiáng)化的零件。
更多關(guān)于滲碳鋼內(nèi)應(yīng)力的殘余的相關(guān)信息、結(jié)構(gòu)用鋼等使用注意事項(xiàng)等,可以參考弘超為您提供的資料,已解決您的問題。
如您有任何疑問:請(qǐng)撥打(0769-82621066,全國(guó)統(tǒng)一服務(wù)熱線:400-699-1286)。